-
Notifications
You must be signed in to change notification settings - Fork 2
Future_Work
This section includes the recommendations for several hardware components which were out of scope this this project. The recommendations for a wheel encoder system and mission command centre telemetry link can be found in the following sections. The hardware components which are still undecided include the mechanical brake, autonomy hardware mounting system, wire harnesses, encoder mounting system.
Final choice: RLS LM13

Selection Criteria
We need to use encoder to get the position and rotational speed of the motors to perform motion estimation and run localization algorithm as well. Initially, an optical encoder sensor along with a custom waterjet cut slotted disk was selected. However, after considering the performance of optical sensors given possible weather conditions (rain, dirt, mud, dust, low light, bright light, etc.) and the effects of the robot’s movement (vibrations and shock, jerk), it was concluded that non-optical encoding system would be necessary. Although a covered optical encoder could address most of the environmental concerns, optical encoders are very sensitive to physical vibrations.
Due to the mechanical constraints, this proved to be a difficult solution to determine as most off-the-shelf magnetic or capacitive encoders require a more with than what is possible given the system (measured to be less than 14mm). The ideal encoder must be resistant to vibrations, must provide adequate resolution (above 1000 points per rotation), and must be rated for the defined maximum speed of 10km/h.
Selection Justification
For a detailed trade study, please refer to Section 7.2.1 in the "Design Specifications" document in Propbot/docs/Reports. The best option so far would be to use the LM13IC10B (readhead) + MR100F085A160E00 (ring) rotary incremental magnetic encoder system, see the figure below for functional information. The ring encoder features a compact sealed readhead and a magnetised ring. The actuator is a periodically magnetised ring with a pole length of 2 mm. Also, the readhead can ride at up to 0.4 mm from the ring’s surface. This system is ideal as a custom mounting system can be designed to fit the slim ring onto the wheel shafts. Further, the system has water-proof sealing to IP68 and is highly resistant to shock, vibrations and pressure.
The mounting system design is still in progress, and so the size of the magnetised ring may differ than the one selected (100mm OD). But the same readhead will be used.
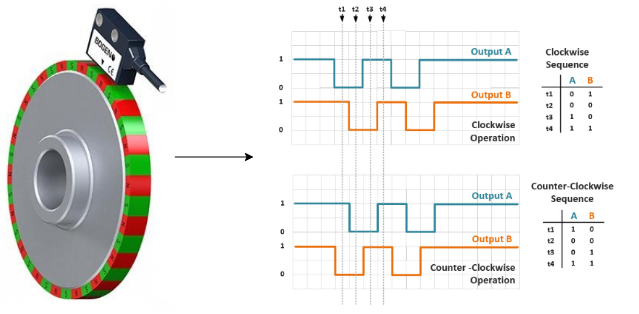
Final choice: Cellular link
Selection Criteria
To allow the robot to transmit telemetry and receive missions, even if it is several kilometers away from the mission command centre, a mission command link option needs to be chosen. This link connects the mission command centre and the PropBot over a wireless connection. The required features for this wireless link are described in the table.
Related Tag(s) | Required Feature | Justification | Specification |
---|---|---|---|
F4.3, NF4.1 |
The distance range is long enough. Minimum of 2 km. |
Since the PropBot will be moving throughout the campus, a long-distance range is necessary. | The link shall still work even if the PropBot is several kilometers away from the mission command centre. |
NF4.1 | The robot shall report operational status at 1 Hz | PropBot needs to move around campus while continuously sending telemetry back to the mission command center. | The link needs high up time. |
NF4.1 |
Sufficient bandwidth for telemetry at 1 Hz Minimum of 16 Kbit/s |
Should have enough bandwidth to transport basic telemetry. | Telemetry reporting should not be constrained by bandwidth. |
Selection Justification
For a detailed trade study, please refer to Section 7.2.2 in the "Design Specifications" document in Propbot/docs/Reports.
After comparing the radio link, WiFi link, and cellular link, the telemetry option we choose is the cellular link. The main driving factor for the decision is the up time/availability. Since the robot drives around campus it is highly likely that buildings will obstruct a radio link that is on the ground. By contrast a cellular connection will work anywhere on UBC campus. WiFi is infeasible due to the poor connection availability outside of buildings. Bandwidth is not really a limiting factor for any of them as we only need to send a very small amount of telemetry data every second (less than 1KB).
Parameter | PM-L45 | OPB625 | LM13IC10B + MR100F085A160E00 |
---|---|---|---|
Optical | Optical | Magnetic | |
5 - 24V | 4.5 - 16V | 4.7-7V | |
NPN - Open Collector | Pull-Up | Incremental, pulse | |
IP 64 | - | IP68 | |
Dependent on disk | Dependent on disk | 1024 counts per turn | |
USD 16.61 | USD 3.03 | USD 85.16 |
Although the optical encoders are significantly less costly than the magnetic encoder, they are barebones sensors that require a custom slotted disk to be made. Further, readings could be compromised due to weather conditions such as rain, dust, mud, etc., all of which are possible operational conditions. Given this, a non-optical sensor is ideal given the encoders will be placed directly by the wheels. Although a custom encoder disk is not necessary for the LM13 as RLS (the manufacturer) provides a great deal of selection when it comes to the magnetised rings. A custom mounting system must designed to mount the rings onto the wheel shafts as well as to secure the readhead. However, this allows the constraint of the wheel shaft space (less than 14mm) to be somewhat avoided.
The main options for telemetry are Wi-Fi, Radio, and Cellular.
Link Type | Wi-Fi | Radio | Cellular |
---|---|---|---|
Low - Close to buildings | Medium - Only within a certain range, and not obstructed | Very High - Available unless heavily obstructed | |
Very High (50+ Mbit/s) | Low (2+ Kbit/s) | Medium to High (1-50 Mbit/s) | |
Unlimited | Unlimited | Limited by Plan |
Integrate new motor drivers
Integrate E-Stop
Integrate situational awareness sensor suite (lidar, RGB-Depth camera)
Integrate positional sensor suite (GPS, IMU)
Integrate cellular adapter
Integrate close range emergency sensors (ultrasonic)
Intergate wheel encoders
This section outlines the outstanding tasks for the software stack.
Object Detection
Track velocity and future path estimation of dynamic obstacles.
Integration with local planner
teb_local_planner
.
Cartographer SLAM
Integrate additional pointcloud from RGB-Depth camera.
Tune Cartographer parameters to optimize performace with the Lidar and RGB-Depth camera.
Add plugins for wireless propagration data collection.
Add the Mapviz
robot_image_plugin
to project robot model on map.
Tune the physics parameters of the Propbot model description (for e.g. mass of model, intertia of the wheels, friction constants).
Add larger simulation environments to execute longer missions.